low-Pressure Plasma
Plasma Technology before Bonding Cleaning of metal Activation of plastics low-Pressure Plasma
Plasma Cleaning of Surfaces
Applications
1. Cleaning of Surfaces (Before Bonding,Soldering Orgluing)
2. Activation of Surfaces ( before printing ,Vanishing,Orgluing)
3.Etching of surfaces(before micro sturucturing of silicon or etching of PTFE) sand blust
4.Deposition of surface -Plasma polymerization. (deposit of hydrophobic/hydrophilic layes)
Deposition of surface -Plasma polymerization. (deposit of hydrophobic/hydrophilic lays)
PLASMA SURFACE MACHINE
How does a low-Pressure Plasma system work?
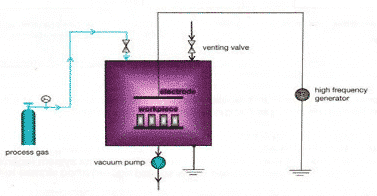

The component for treatment is exposed to plasma. The plasma system receives continuously fresh gas whilst contaminated gas is sucked off.
One option of varying parameters is the volume of the recipient. The chamber size is configured according to size quantity of the component to be treated. Large recipients can have a volume of 10,000 ltrs and more. Laboratory systems have a volume in the range of 1 to 50 ltrs. The method of plasma creation
Standard applications are carried out without charge.
Plasma Technology
Examples of sample parts / product groups









Applications
Cleaning
1.1 Cleaning of metal
Some components are covered with grease, oils, wax and other organic or inorganic contaminants (also oxide layers)
a) Soldering under vacuum: no flux is required
b) Long-term stored electrical components, which have oxidized over time. Oxidation can be eliminated by hydrogen plasma.
Bonding:
Often organic contaminants, in example, residual of Electroplating processes, of adhesives, of flux residuals. disturb bonding. this can be removed by plasma. (oxide layers can worsen the bonding process.)
2. Activation of plastics
Polypropylene of PTFE (Polytetrafluoroethylene) are themselves of homopolar structure.






3. Etching



3.1 Etching of metals
Aluminium using chlorine
3.2 Etching of plastics
Etching is very important with plastics, which are difficult to lacquer and to glue, like POM or PTFE.


4. Coating by plasma polymerization



Technical data
Power supply
Width 562 mm (22.15“)
Height 211 mm (8.31“)
Depth 420 mm (16.54“)
Weight
20 kg (44 lbs)
Plasma head
Length 180 mm (7.09“)
Width 60 mm (2.36“)
Thickness 40 mm (1.57“)
Weight 0.5 kg (1 lbs)
Width of treatment
Approx. 50 – 60 mm (1.97“ -2.37“) (per nozzle)
Flexible tube
2x Plastic- metal protective tube
Length approx. 3 m (118.11“)
Diameter approx. 19 mm (0.75“)
Bending radius 100 mm (3.94“)
Generator frequency
Approx. 40 kHz
Power
Approx. 500 W (per nozzle)
Supply voltage
230 V AC, 50/60 Hz (per nozzle)
Manual operation
About elements on the front panel
Halbautomatische Steuerung
Remote control through D-SUB connector on the
rear panel of the supply unit
Automatic microcontroller controlled
Process monitoring (factory set)
Pulse width
Electrical current
Air production
Contact protection function
This device is to be used only on non
conductive surfaces.